Next-Level Composite Production
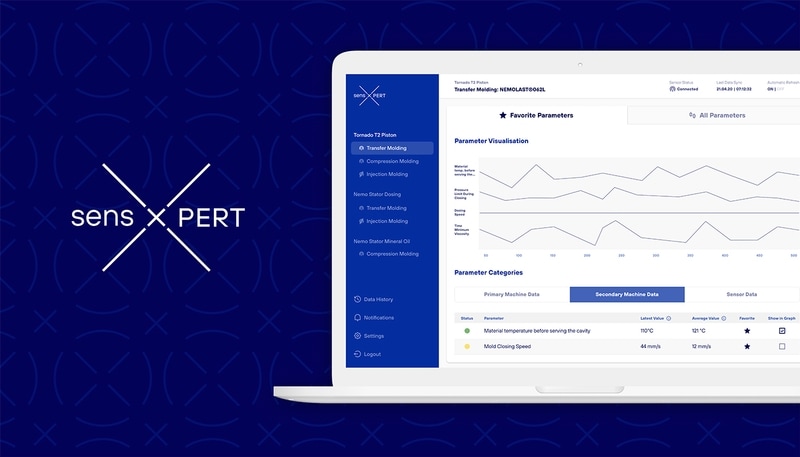
Next-Level Composite Production: Sustainable, Highly Productive, Efficient
As we continue to move towards a world where our streets will see more and more electric vehicles, composite materials continue to move into the spotlight. Batteries in cars significantly contribute to the total weight and thus limit the driving range. This forces engineers to reduce weight of other components in the car. The lighter the vehicle, the longer can it run.
Composites are a preferred material as they can be adapted to a wide range of different applications. For electric vehicles (EVs), their durability, resistance to chemicals and corrosion and high performance at elevated temperatures are especially valuable.
CosiMo: Leveraging machine learning for efficient high-volume production
The three-year CosiMo research project, funded by the Bavarian government, started in June 2018 and brings together the University of Augsburg (MRM & ISSE), the German Aerospace Center, ITA Augsburg and industrial partners including KUKA, Faurecia, Premium Aerotec, Krauss-Maffei, SGL-Carbon, NETZSCH, Siebenwurst and IBA.
The objective is to manufacture components in their final shape in a single process step using the compression-RTM technology for the in-situ polymerization from ɛ-Caprolactam to polyamide 6. This, in turn, enables sustainable and cost-effective production of lightweight components in the automotive and aircraft construction industries.
Based on this goal, key topics of the CosiMo project are:
- the impregnation of recycled glass-fiber nonwoven materials by in situ polymerization
- the integration of reinforcement structures alongside the load paths and metal inserts
- the application of sensor-based process monitoring systems to collect process data, and
- the development of virtual models of machines and processes using machine learning methods
More information about the project is available on the website of the University of Augsburg and the German Aerospace Center (DLR).
sensXPERT contributes to the sensor-based process monitoring system
During production of a part with a complex geometry, all process steps are monitored continuously using a sensor network jointly developed with project partners which aims at assuring the required quality of the components in real-time.
Integrated in the mold, durable sensors from sensXPERT measure crucial material properties and thus detect the flow front as well as polymerization of the resin.
The data from all sensors is combined to analyze the real polymerization behavior and to optimize simulation models. This way, the quality of the part can be monitored in real-time and in the mold. The downstream quality assurance step can be eliminated generating significant time and resource savings.
Leveraging the power of machine learning
The real-time data gathered by the in-mold sensors is processed using machine learning techniques.
Based on material science, the underlying model continuously predicts the polymerization of the part based on the real-time material behavior. Thus, quality defects can be anticipated and the production process can be adapted to prevent low-quality parts and scrap.
Total transparency of manufacturing processes
All data is displayed and stored in the sensXPERT cloud software. In customizable dashboards, it is possible to observe the real-time polymerization of each part and compare different processes and production plants equipped with the sensXPERT solution. This is possible from anywhere and from any device.
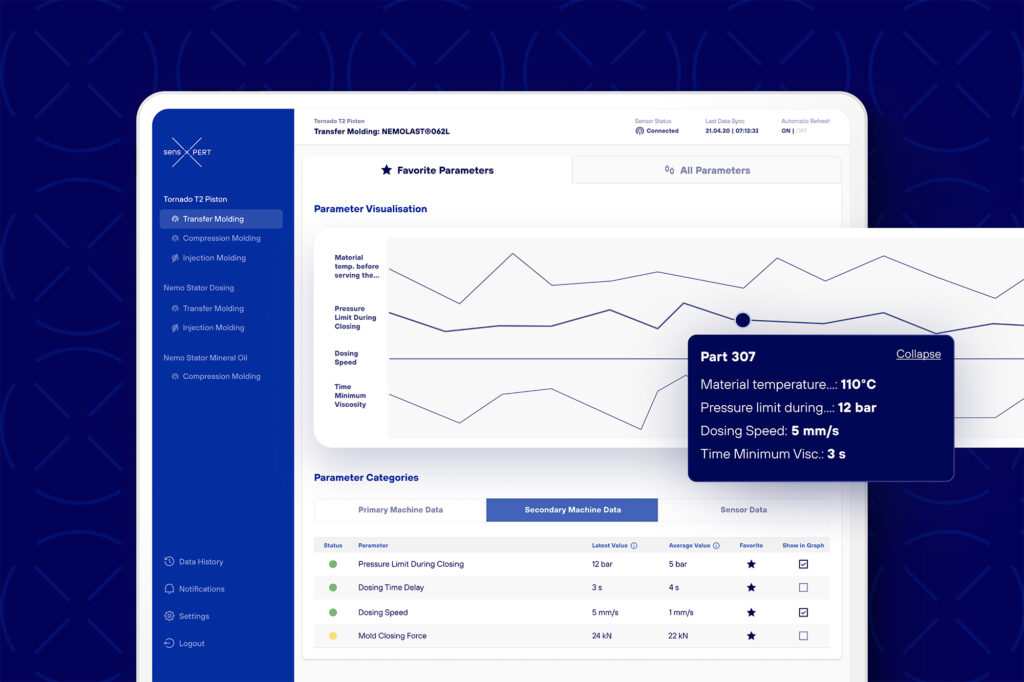
Sustainable, highly productive, efficient
In the CosiMo project, sensXPERT contributes significantly to the research in the production of high-quality composite components. The solution allows for a highly productive and efficient production which translates into significant time and resource savings. By reducing scrap production, a significant step towards a more sustainable plastic production can be realized at the same time.
Sources
Center for Lightweight-Production-Technology – CosiMo – Composites for sustainable Mobility (dlr.de)